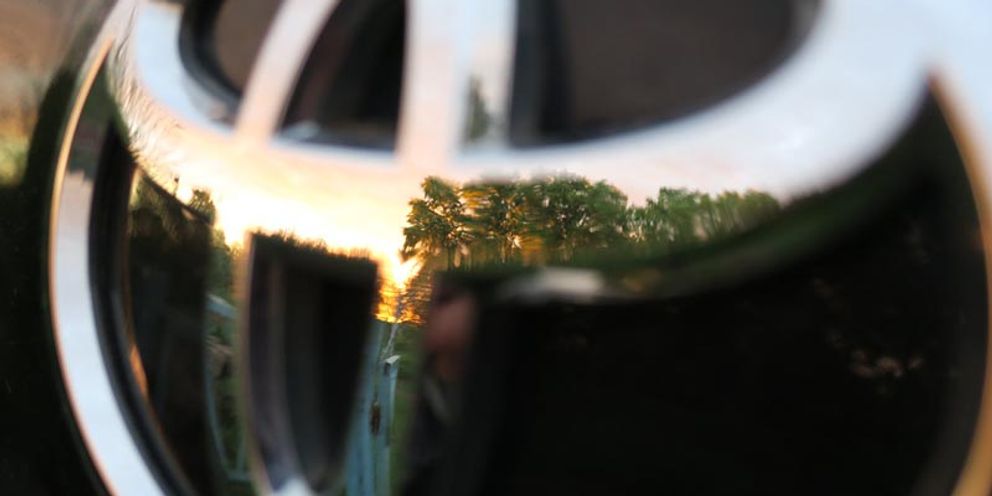
History of the Toyota Production System
Image Source: Pixabay
Written by Gregory Miller
The Toyota Production System (TPS) is the epitome of efficiency in the workplace. The TPS follows the philosophy of “the complete elimination of waste.” This philosophy is demonstrated in Toyota’s highly efficient production process. Over the years, the TPS has morphed and improved through the fires of trial and error in a bid to make the workplace a hyper-efficient environment. The TPS system was modeled after the “Just-in-Time” concept that was developed by the founder of Toyota Motor Corporation, Toyoda.
In many cases, waste can show up in the workplace in the form of excess inventory, defective products, and unnecessary processing steps. In other words, all excess is considered wasteful. Furthermore, it’s believed that all elements of waste can combine with one another to create more waste. As the waste builds over time, it can even affect the management of a corporation.
TPS can trace its roots back to the automatic loom created by Sakichi Toyoda. The automatic loom automated completed processes that previously could only be performed manually. It could also form judgments on its own, making the invention revolutionary. Through the automatic loom, Sakichi improved both work efficiency and productivity. Kiichiro Toyoda also set out to breathe life into the idea of eliminating waste within the workplace. It was Kiichiro who came up with techniques and methodologies that led to waste elimination between operations. Thus the “Just-in-Time” method was born.
Goals
TPS has always had primary objectives that it strived to meet such as designing out overburden and inconsistency while eliminating waste. The most vital effects on process value delivery are accomplished by devising a process capable of fulfilling the required results in a smooth manner. This is done by eliminating inconsistency, which is also known as“design out” inconsistency. The process must have enough flexibility that it does not overburden anyone to generate waste. The small improvements in waste reduction are benefits to any corporation. Ultimately, there are eight types of waste that the TPS addresses:
1) Waste of making defective products
2) Waste of underutilized workers
3) Waste of overproduction (considered to be the largest waste)
4) Waste of transportation
5) Waste of time on hand (waiting)
6) Waste of stock at hand
7) Waste of processing itself
8) Waste of movement
History
It all began in 1945. Kiichiro Toyoda issued a challenge to his company to “catch up to America”. However, post-war Japan was low on resources while America was not. America specialized in the mass production model in which thousands of identical pieces and parts were manufactured to gain economies of scale. In Japan, duplicating a similar business model was simply not possible because the public was interested in variety, materials were a rare sight and orders were never reliable.
Kiichiro Toyoda began to envision a system in which all essential parts for assembly at the warehouse would arrive “Just-in-Time” for when they were needed. After all, there were no extra parts to spare at the time. Kiichiro knew that such a system would never work by stockpiling these parts at a warehouse. The parts would be made when they were needed. That way, the potential for the generation of waste would be greatly reduced. In 1962, Toyota implemented the Toyota Production System, but Kiichiro Toyoda died a decade before he could see his dream become a reality.
Taiichi Ohno
Taiichi Ohno was one of the first people to step up when Kiichrio Toyoda issued his challenge to catch up to America. A machine shop manager, Taiichi utilized his ingenuity and genius to eventually develop the TPS. Taiichi realized that there was much to be learned from American auto manufacturers and began studying Ford’s production system and gained an understanding of American inventory processes. Adding his expertise of spinning and weaving to what he learned from Ford, he began to slowly develop a new process. The development of the Toyota Production System was a long and arduous process that took years of experimentation and trial and error. As Ohno was given more responsibility, he began spreading his ideas throughout the company.
Ohno explains in his book, “Toyota Production System,” that the system rested on two pillars: automation and Just-in-Time flow. He’s also noted saying that the TPS was “a system for the absolute elimination of waste”. Ohno was able tosucceed because he had the support of Eiji Toyoda, who was in a position of management at the time after his cousin Kiichiro left the company in 1950.
Autonomation
Automated looms can work without weavers present because the looms can detect when something is wrong and shut themselves down automatically. The beauty of autonomation, known as Jidoka in Japanese, is that workflow is set up in such a way that even when the smallest problem is detected, work comes to a halt, and the problem is fixed before work resumes once more. This concept is also known as “stop-the-line.”
Taiichi Ohno defined the term "autonomation" best: “automation with a human touch”. He makes the analogy that the process of autonomation is much like the human body, complete with a nervous system that ensures that heartbeat, digestion, and breathing work properly. Drawing upon the same analogy, if our body senses danger, such as taking a bite of extremely hot food, our autonomic nervous system will cause us to withdraw the food from our mouth before a signal is even sent to the brain to await instructions. The process of autonomation is much the same in which the reflexes of a corporation or organization will react and correct abnormalities that may arise quickly and efficiently without the need of sending a message to the “brain” to wait for instructions.
Shigeo Shingo
Shigo Shingo was a consultant who was also essential to the implementation of the Toyota Production System. Shingo helped companies worldwide understand and integrate the system. During the 1980s, those who implemented Just-in-Time manufacturing were given a “Green Book.” It was the first book that covered the concept of Just-in-Time in English. It was terribly translated, highly technical and heavy, but it allowed foreign companies to gain insight into what made this process so successful for Toyota. The book, written by Shingo, covered two main points: zero inspection and non-stock production.
Non-stock Production
Non-stock production is exactly as it sounds. It means keeping no stock on hand and ordering parts when they’re needed. Just-in-Time flow eliminated the need to stockpile inventory, which is an essential component of a business plan that involved economies of scale. The focus of non-stock production was to make parts in small batches. To accomplish this task as efficiently as possible, machines had to be capable of manufacturing multiple types of inventory parts.
Zero Inspection
For the concept of autonomation to work correctly, all processes used in the production process must be designed to be free of mistakes. There shouldn’t have to be a position for an individual to examine manufacturing machines to ensure that they're working fine, nor should there be an individual who examines a tested product to see if its “good”. A system free of mistakes would not require inspections of any kind.
Sharing the system
Toyota truly began sharing the TPS system with others in the 1990s. Toyota originally shared the system with their suppliers, but as more and more companies became interested, the company began offering instruction to others. Toyota has even donated its engineers to charity events to teach them the ways of the TPS so that non-profits could increase their efficiency thus increasing their capacity to help more people in need. Take for example, when Toyota assisted the Food Bank For New York City to considerably reduce the wait times at food pantries, the time it took to pack items at a food distribution center and wait times at soup kitchens.
A Worldwide Phenomenon
Today, thousands of people practice the concepts introduced by the Toyota Production System. With this process, individuals and corporations alike learn the philosophies of “good thinking”, “daily improvements”, and “good products”. The result has created thousands of highly efficient businesses that have eliminated unnecessary and wasteful processes. Today, Toyota works tirelessly to continue to improve and evolve the TPS, so that it continues to stay relevant in an ever-evolving world.
Updated